Applicable to Models: SAT 3600, SAT 3700, SAT 3701, SAT 3702, SAT 3703, SAT 3800, SAT 3801, SAT 3802
STi5518 functional modules
a. Central processor
The STi5518 Central Processing Unit is a ST20C2+ 32-bit processor core. It contains instruction processing logic, instruction and data pointers, and an operand register. It directly accesses the high-speed on-chip SRAM, which can store data or programs and uses the cache to reduce access time to off-chip program and data memory.The processor can access memory via the Programmable CPU Interface (often referred to as the EMI) or the Shared Memory Interface (SMI), which is shared with the video, audio, sub-picture and OSD decoders.
MPEG video decoder
This is a real-time video compression processor supporting the MPEG-1 and MPEG-2 standards at video rates up to 720 x 480 x 60 Hz and 720 x 576 x 50 Hz. Picture format conversion for display is performed by vertical and horizontal filters. User-defined bitmaps can be super-imposed on the display picture by using the on-screen display function. The display unit is part of the MPEG video decoder, it overlays the four display planes.
The display planes are normally overlaid in the order illustrated, with the background color at the back and the sub-picture at the front (used as a cursor plane). The sub-picture plane can alternatively be positioned between the OSD and MPEG video planes where it can be used as a second on-screen display plane.
Audio decoder
The audio decoder accepts: Dolby Digital, MPEG-1 layers I, II and III, MPEG-2
layer II 6-channel, PCM, CDDA data formats; MPEG2 PES streams for MPEG-2,
MPEG-1, Dolby Digital, MP3, and Linear PCM (LPCM). The audio decoder supports DTS® digital out (DVD DTS and CDDA DTS). SPDIF input data
(IEC-60958 or IEC-61937 standards) is accepted if an external circuitry
extracts the PCM clock from the stream. Skip frame, repeat blocks and soft mute frame features can be used to synchronize audio and video data.
PTS audio extraction is also supported. The device outputs up to 6 channels of
PCM data and appropriate clocks for external digital-to-analog converters. Programmable downmix enables 1,2,3 or 4 channel outputs. Data can
be output in either I²S format or Sony format. The decoder can format output
data according to IEC-60958 standard (for non compressed data: L/R channels, 16, 18, 20 and 24-bits) or IEC-61937 standard (for compressed data),
for FS = 96 kHz, 48 kHz, 44.1 kHz or 32 kHz. Sampling frequencies of 96 kHz, 48
kHz, 44.1 kHz, 32 kHz and half sampling frequencies are supported.
A down sampling filter (96 kHz/48 kHz) is available. The decoder supports dual
mode for MPEG and Dolby Digital. It includes a Dolby surround compatible downmix
and a ProLogic decoder. A pink noise generator enables the accurate positioning of speakers for optimal surround sound setup. PCM beep
tone is a special mode used for Set Top Box. It generates a triangular signal
of variable frequency and amplitude on the left and right channels. In global mute mode, the decoder decodes the incoming bitstream normally but the
PCM and SPDIF outputs are soft muted. This mode is used to prepare a period of
decoding mode, to synchronize audio and video data without hearing the audio. Slow-forward and fast-forward trick modes are available for
compressed and non-compressed data. The control interface of the decoder is
activated via memory mapped registers in the ST20 address space.
IR transmitter/receiver
The STi5518 provides a pulse-position modulated signal for automatic VCR
programming by the set-top box. The signal is output to the IR blast pin and an
accessory jack pin, simultaneously. The pulse frequency, number of pulses (envelope length) and the total cycle time is controlled by registers.
Modem analog front-end interface
The Modem Analog Front-end interface is used to transfer transmit and receive
DAC and ADC samples between the memory and an external modem analog front-end
(MAFE), using a synchronous serial protocol. DMA is used to transfer the sample
data between memory buffers and the MAFE interface module, with separate
transmit and receive buffers and double buffering of the buffer pointers. FIFOs
are used to take into account the access latency to memory, in a worst case system and to allow the use of bursts for memory
bandwidth efficiency improvement. The V22 bis standard is supported.
Memory subsystem
On-chip
The on-chip memory includes 2Kbytes of instruction cache, 2Kbytes of data cache
and 4Kbytes of SRAM that can be optionally configured as data cache. The
subsystem provides 240M/bytes of internal bandwidth, supporting pipelined 2- cycle internal memory access. The instruction and data caches are
direct-mapped, with a write-back system for the data-cache. The caches support
burst accesses to the external memories for refill and write-back. Burst access increases the performance of pagemode DRAM memories.
Off-chip
There are two off-chip memory interfaces:
• The external memory interface (EMI) accessed by the ST20 is used for the
transfer of data and programs between the STi5518 and external peripherals,
flash and additional SDRAM and DRAM.
• Shared memory
interface (SMI) controls the movement of data between the STi5518 and 16, 32 or
64 Mbits of SDRAM. This external SDRAM stores the display data generated by the
MPEG decoder and CPU and the C2+ code data. The EMI uses minimal external
support logic to support memory subsystems, and accesses a 32 Mbytes of
physical address space (greater if SDRAM or DRAM is used) in four general
purpose memory banks of 8 or 16 bits wide, 21 or 22 address lines, and byte
select. For applications requiring extra memory, the EMI supports this extra
memory with zero external support logic, even for 16-bit SDRAM devices. The EMI
can be configured for a wide variety of timing and decode functions by the
configuration registers. The timing of each of the four memory banks can be set
separately, with different device types being placed in each bank with no need
for external hardware.
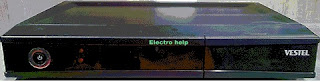
Serial communication
Asynchronous serial controllers
The Asynchronous Serial Controller (ASC), also referred to as the UART
interface, provides serial communication between the STi5518 and other
micro-controllers, microprocessors or external peripherals. The STi5518 has four ASCs, two of which are generally used by the Smart card controllers. Eight or nine bit data transfer, parity
generation, and the number of stop bits are programmable. Parity, framing, and overrun
error detection increase data transfer reliability. Transmission and reception
of data can be double-buffered, or 16-deep FIFOs can be used. A mechanism to
distinguish the address from the data bytes is included for multiprocessor
communication. Testing is supported by a loop-back option. A 16-bit baud-rate
generator provides the ASC with a separate serial clock signal. Two ASCs
support full-duplex and 2 half-duplex asynchronous communication, where both
the transmitter and the receiver use the same data frame format and the same
baud rate. Each ASC can be set to operate in Smartcard mode for use when
interfacing to a Smartcard.
Synchronous serial controller
Two Synchronous Serial Controllers (SSC) provide high-speed interfaces to a
wide variety of serial memories, remote control receivers and other
micro controllers. The SSCs support all of the features of the Serial Peripheral Interface bus (SPI) and the I2C bus. The SSCs can be programmed to interface to
other serial bus standards. The SSCs share pins with the parallel input/output
(PIO) ports, and support half-duplex synchronous communication.
Front-end interface
The STi5518 can be connected to a front-end through the following interfaces:
• I2S interface;
• multi-format serial interface;
• multi-format parallel interface;
• ATAPI interface (for Hard Disk Drives and DVD-ROMs)
On-chip PLL
The on-chip PLL accepts 27 MHz input and generates all the internal
high-frequency clocks needed for the CPU, MPEG and audio subsystems.
Diagnostic controller (DCU)
The ST20 Diagnostic Controller Unit (DCU) is used to boot the CPU and to
control and monitor the chip systems via the standard IEEE 1194.1 Test Access
Port. The DCU includes on-chip hardware with ICE (In Circuit Emulation) and LSA
(Logic State Analyzer) features to facilitate verification and debugging of
software running on the on-chip CPU in real time. It is an independent hardware
module with a private link from the host to support real-time diagnostics.
Interrupt subsystem
The interrupt system allows an on-chip module or external interrupt pin to
interrupt an active process so that an interrupt handling process can be run.
An interrupt can be signalled by one of the following: a signal on an external interrupt pin, a signal from an internal peripheral or subsystem, software
asserting an interrupt in the pending register. Interrupts are implemented by
an on-chip interrupt controller and an on-chip interrupt-level controller. The interrupt controller supports eight prioritized interrupts as inputs and
manages the pending interrupts. This allows the nesting of pre-emptive
interrupts for real-time system design. Each interrupt can be programmed to be
at a
lower or higher priority than the high priority process queue.
PAL/NTSC/SECAM encoder
The integrated digital encoder converts a multiplexed 4:2:2 or 4:4:4 YCbCr
stream into a standard analog base-band PAL/NTSC or SECAM signal and into RGB,
YUV, Yc and CVBS components. The encoder can perform closed caption, CGMS
encoding, and allows MacrovisionTM 7.01/6.1 copy protection. The DENC is able
to encode Teletext according to the “CCIR/ITU-R Broadcast Teletext System B”
specification, also known as “World System Teletext”. In DVB applications, Teletext data is
embedded within DVB streams as MPEG data packets. It is the responsibility of
the software to handle incoming data packets and in particular to store
Teletext packets in a buffer, which then passes them to the DENC on request.
Smart-card interfaces
Two Smartcard interfaces support Smartcards compliant with ISO7816-3. Each
interface is has a UART (ASC), a dedicated programmable clock generator, and
eight bits of parallel IO port.
PWM and counter module
The PWM and counter module provides three PWM encoder outputs, three PWM
decoder (capture) inputs and four programmable timers. Each capture input can
be programmed to detect rising edge, falling edge, both edges or neither edge (disabled). These facilities are clocked by two independent
clocks, one for PWM outputs and one for capture inputs/timers. The PWM counter
is 8-bit, with 8-bit registers to set the output-high time. The capture/compare
counter and the compare and capture registers are 32-bit. The module generates
a single interrupt signal.
Parallel I/O module
44 bits of parallel I/O are configured in 6 ports, and each bit is programmable
as output or input. The output can be configured as a totem-pole or open-drain
driver. The input compare logic can generate an interrupt on any change of any
input bit. Many parallel IO have alternate functions and can be connected to an
internal peripheral signal such as a UART or SSC
POWER
BOARD (16PW07 E3)
The TOPSwitch concept is used for power supply. TOP 233Y (IC1) is designed to
work until 50 Watts in family of TOPSwitch_FX with 5 pins. The receiver works
between 85 and 265 VAC mains voltage by using TOP 233Y in SMPS (Switch Mode
Power Supply). The secondary voltage regulation is adjusted by changing the
duty cycle of drain signal according to the feedback voltage, which is got from
the secondary side of transformer. The feedback voltages are 3.3V and 5V. This
is connected to the comparator pin of TOP 233Y (IC1-pin1) via IC12 (Optocoupler).
The comparator pin also protects the box against short circuits and overload.
The Vcc voltage of IC1 is between 2V –3V at pin2. The TOP 233Y works at a fixed
frequency. This frequency is fixed by RC oscillator at pin1. The pin3 and pin 4
are ground and the pin5 is drain of MOSFET, which is inside the TOP 233Y.
The
switching of LNB supply voltage is done here. 18V and 22V outputs of
transformer switched by Q1, Q2 and H/V output of STV299 (TU400). By this way
overheating and unnecessary power consumption of Q5 (BD235) that regulates the
LNB supply is prevented.
22kHz tone which is needed for DiSEqC signals, is generated at pin15
(Alps-TU400) or pin12 (Sharp-TU400) of STV0299 in tuner 22KHz is added to LNB
supply here via LM358N (IC4).
MAIN BOARD (16MB07 E3 )
The main board contains two parts: Front-end and Back-end. The digital signal is demodulated in Front-end and then decoded in Back-end. Analog signals are processed in different part.
The tuner (TU400 Alps or Sharp) is capable of getting both digital broadcasts. After the modulated signals (I, Q outputs) receive from tuner, they go to STV0299 for demodulation process in tuner. (TU400) In this IC, QPSK (Quadrated Phase Shift Keying) demodulation and Forward Error Correction (FEC) are done which is necessary to demodulate DVB-S transmission. TS (transport stream): The multiplexed digital stream which includes video, audio and data information related to more than one channel (can be only one channel for SCPC signals) and DVB tables. TS signals which are generated after demodulation, reach to Sti5518 (IC100) via 8 bits data bus. However, Byte Clock (TSIn_BCLK), Packet Clock (TSIn _STROUT) signals are also sent to ST5518 (IC100) for demultiplexing process of TS. STV0299 is controlled by I2C. In addition, 22kHz tone which is needed for DiSEqC signals, is generated at pin12 (Alps) or pin10 (Sharp) of STV0299 in tuner.
LNB supply voltage (13/18V) is regulated via power board. Switching of supply voltage between LOOP_IN and LNB_SUPPLY is done by Q402 transistors. The voltage on R403 is proportional with the current of LNB supply. Overload on LNB supply increases the voltage on R403, which results switching of Q400, Q401. By this way input LNB_OVERLOAD signal port of Sti 5518 (IC100) has the knowledge of LNB overload and then LNB supply is cut off for protection of box via Sti 5518 port (P25).
At the backend part, there is a 32-bit CPU ST20 (in Sti 5518 embedded) that controls all processes. Demultiplexer of the CPU provides the transmission of the desired channel’s information from TS (Transport Stream) to MPEG Decoder section. The program that runs on Sti5518 is in Flash memories (IC301). 8Mbits SDRAM (IC300) is used for data memory of this program.
ST20 uses 32- bit data and 22- bit address buses for access to flash, DRAM and MPEG decoder. It uses RAS, CAS etc. (read, write, enable) signals to activate related IC while accessing them.
The clock which is needed by Sti 5518 (IC100), is generated at power on mode by 27MHz crystal (X100) and IC102 (74HCU04). The output of PWM outputs of Sti 5518 (IC100), is filtered to have a DC level via R129 and C118. At the output of ICS3, the 27MHz clock can be adjusted according to capacity of pins of 27MHz crystal to ground. This capacity is related with DC value on D100 and D101 (BB133) at pins of crystal. This operation maintains synchronization between audio-video that are coming from MPEG transport stream and PCR clock.
Sti 5518 (IC100) can communicate any micro controller via RS232 by using IC101 (MAX232- RS232 level converter). The RS232 output of receiver is used for debug any problem using Windows Hyper Terminal program.
MPEG decoder in Sti 5518 (IC100), is responsible for decoding of MPEG video and audio signals. The video, which is compressed using MPEG2 and audio, which is compressed using MPEG1 Layer 1-2, are processed here. After decoding, CCIR 601 formatted 8-bit video and PCM formatted audio, are generated by mpeg decoder. If digital broadcast has a teletext information, Sti 5518 (IC100) inserts teletext info into VBI (vertical blanking interval) which can be watched on TV. Digital audio that is PCM formatted on Sti 5518’ s output, is processed by CS4335 (IC500) and amplified by LM833 (IC501) and then switched through IC200 (M74HC4052).
In digital mode, RGB signals are only delivered to TV scart. CVBS output is distributed through IC201 (M74HC4052) to TV, AUX/VCR and VCR scarts. When VCR becomes active, audio and video signals are driven to TV and VCR scarts, which is activated by pin8 of VCR scart.
The program information is stored in 128Kbits EEPROM (24C128 – IC302) via I2C.
How to enter the service mode - SERVICE MENU INTERFACE
There is a service menu for service person which is accessed by entering “MAIN MENU” then pressing “9”, “2”, “9”, “5”, “2”, “6” keys on the remote control. You will see service menu on the screen. This menu consists of fifteen active lines.
RF Modulator System
You can control RF modulator system at this line. RF modulator system option can be selected as Pal G or Pal I or Pal K type in software side by pressing left or right cursor key on the remote control.
RF Modulator Type
You can control RF modulator type at this line. RF modulator option can be selected as Sharp or Samsung or LG type in software side by pressing left or right cursor key on the remote
control.
Tuner Type
You can control Tuner type in software version at this line
Scarts
You can control number of scarts in software version at this line Reboot : You press OK button on the remote commander. Apparatus is restart.
Clear
Database
You press OK button on the remote commander. These settings reinitialize whole EEPROM
and store all programs erase.
L/R: DBCopy – OK: Upload PGM
The object of this manual is to give necessary information and details to the
user to UPLOAD the program table to the receiver through RS232.
The list of the necessary equipment is as follows:
• Receiver and TV
• PC with “Hyper Terminal” function,
• RS232 serial communication cable (male to female modem cable).
Steps to be followed by the user are given below
1. Connect the serial communication cable between the RS232 outport of the
receiver and the serial communication port (COM1 or COM2) of the PC.
2. Make sure that the PC is on and the receiver is in Power on mode.
3. Run “Hyper Terminal” program of the PC from Start / Programs / Accessories /
Communications / Hyper Terminal menu.
4. For a new connection, run Hypertrm.exe file.
5. Give a name and choose an icon for the connection. (You do not need to make
a new connection every time. You can use this name for the future connections.)
6. Choose communication port in the new coming window (COM1 or COM2) whichever
you have used in Step 1.
7. Port settings should be as follows:
Bits per second : 38400
Data Bits : 8
Parity : None
Stop bits : 1
Flow control : None
8. Now Hyper Terminal connection is established.
9. Go to “L/R: DBCopy – OK: Upload PGM” line on the service menu and press
“LEFT” or “RIGHT” keys of remote control (for copying database to the
receiver). Please wait until the print statements on the Hyper Terminal screen
end.
10. From “Transfer” menu, choose “Receive File”.
11. Choose 1K Xmodem as protocol type.
12. “L/R: DBCopy – OK: Upload PGM” line on the service menu and press “OK” key
of remote control. Then Receive on of Hyper Terminal window and enter a file
name like (Program_table.pit) and press “OK” button. then You will see the
progress on the PC screen. Besides, on TV screen the receiver will count the
downloaded packets.
13.
Wait for the transfer to be completed. Then, disconnect and exit from Hyper
Terminal window.
Download PGM
The object of this manual is to give necessary information and details to the
user to upgrade the program table of the receiver through RS232.The list of the
necessary equipment is as follows:
• Receiver and TV
• PC with “Hyper Terminal” function,
• RS232 serial communication cable (male to female modem cable).
Steps to be followed by the user are given below:
1. Connect the serial communication cable between the RS232 outport of the
receiver and the serial communication port (COM1 or COM2) of the PC.
2. Make sure that the PC is on and the receiver is in Power on mode.
3. Go to “ Clear Database ” line and press “OK” key and then wait for twenty
seconds (old program table is deleted).
4. Run “Hyper Terminal” program of the PC from Start / Programs / Accessories /
Communications / Hyper Terminal menu.
5. For a new connection, run Hypertrm.exe file.
6. Give a name and choose an icon for the connection. (You do not need to make
a new connection every time. You can use this name for the future connections.)
7. Choose communication port in the new coming window (COM1 or COM2) whichever
you have used in Step 1.
8. Port settings should be as follows:
Bits per second : 38400
Data Bits : 8
Parity : None
Stop bits : 1
Flow control : None
9. Now Hyper Terminal connection is established. From “Transfer” menu, choose
“Send File”.
10. Enter file name to be sent (program table).
11. Choose 1K Xmodem as protocol type.
12. Press Send button of Hyper Terminal window and then Go to “Download PGM”
line on the service menu and press “OK” key of remote control. You will see the
progress on the PC screen. Besides, on TV screen the receiver will count the
downloaded packets.
13. Wait for the transfer to be completed. Then, disconnect and exit from Hyper
Terminal window.
Reset receiver by re-plugging in the mains cord of the set to the mains supply.
Receiver will tune to new program table.
You press “OK” button remote commander to enter Remote/Front panel test then you can see name of the button on the front panel or remote commander you pressed. By pressing Menu button on the remote commander two times, you can exit.
7-Segment Display Test
You press the OK key on the remote commander to start 7-segment display test. You can see the test pattern on the display.
System Diagnostic
You press the OK key on the remote commander and show your IC information in apparatus main hardware
Development Team
You press the OK key on the remote commander and Show your development team list Upload Default Sat_Xpdrs :
This line can explain information under line
Download Default Sat_Xpdrs :
The object of this manual is to give necessary information and details to the user to transmission the program table and preset table to the receiver through RS232.
The list of the necessary equipment is as follows:
• Receiver (master that sends the program table), TV
• Receiver (slave that receives the program table), TV
• RS232 serial communication cable (male to male modem cable).
Steps to be followed by the user are given below
1. Connect the serial communication cable between the RS232 outport of the receiver to other receiver.
2. Make sure that both receivers are in Power on mode.
3. Open the “main menu” and press “929526” keys sequentially for both of the receivers, you will see service menu on the TV screens.
4. Go to “L/R: DBCopy – OK: Upload PGM” line on the service menu for master receiver and press “LEFT” or “RIGHT” keys of remote control (for copying database to the receiver).
5. Go to “Download PGM” line on the service menu for slave receiver
6. “L/R: DBCopy – OK: Upload PGM” line on the service menu and press “OK” key of remote control for master device. “Download PGM” line on the service menu and press “OK” key of remote control for slave device. Besides, on TV screen the receiver will count the downloaded packets.
7. Wait for the transfer to be completed the program table for both receivers.
8. Power off both receivers then power on them.
9. Open the “main menu” and press “929526” keys sequentially for both of the receivers, you will see service menu on the TV screens.
10. Go to “Upload default Sat_Xpdrs” line on the service menu for master receiver.
11. Go to “Download default Sat_Xpdrs” line on the service menu for slave receiver
12. “Upload default Sat_Xpdrs” line on the service menu and press “OK” key of remote control for master device. “Download default Sat_Xpdrs” line on the service menu and press “OK” key of remote control for slave device. Besides, on TV screen the receiver will count the downloaded packets.
13. Wait for the transfer to be completed the preset table for both receivers.
Rs232
Test
You connect the jumper to Rx output and Tx output. You press the “OK” key on
the remote commander then you can see “tESt” at the front display. You release
the “OK” key on the remote commander then you can see “Err” at the front
display.
You can return to main menu by pressing “Menu” keys on the remote control.
SOFTWARE UPGRADE THROUGH RS232 FOR HAVİNG 7-SEGMENT DISPLAY MODELS
The object of this manual is to give necessary information and details to the user to upgrade the software of the receiver through RS232.
The list of the necessary equipment is as follows:
Receiver and TV
PC with “Hyper Terminal” function,
RS232 serial communication cable (male to female modem cable).
Steps to be followed by the user are given below
1. Connect the serial communication cable between the RS232 out port of the receiver and the serial communication port (COM1 or COM2) of the PC.
2. Make sure that the PC is on and the receiver is in the Standby mode.
3. Run “Hyper Terminal” program of the PC from Start / Programs / Accessories / Communications / Hyper Terminal menu.
4. For a new connection, run Hypertrm.exe file.
5. Give a name and choose an icon for the connection. (You do not need to make a new connection every time. You can use this name for the future connections.)
6. Choose communication port in the new coming window (COM1 or COM2) whichever you have used in Step 1.
7. Port settings should be as follows:
Bits per second : 115200
Data Bits : 8
Parity : None
Stop bits : 1
Flow control : None
8. Now Hyper Terminal connection is established. From “Transfer” menu, choose “Send File”.
9. Enter file name to be sent.
10. Choose Xmodem1K as protocol type.
11. Get the receiver out of standby mode using front panel keys just after pressing Send button at the hyper terminal window. You will see the progress on the PC screen. Besides, front panel display of the receiver will count the downloaded packets.
12. Wait for the transfer to be completed. Then, disconnect and exit from Hyper Terminal window.
Receiver will automatically start to operate.
SOFTWARE
UPGRADE THROUGH RS232 FOR HAVING LED MODELS
The object of this manual is to give necessary information and details to the
user to upgrade the software of the receiver through RS232.
The list of the necessary equipment is as follows
Receiver and TV
PC with “Hyper Terminal” function,
RS232 serial communication cable (male to female modem cable).
Steps to be followed by the user are given below:
1. Connect the serial communication cable between the RS232 out port of the
receiver and the serial communication port (COM1 or COM2) of the PC.
2. Make sure that the PC is on.
3. Run “Hyper Terminal” program of the PC from Start / Programs / Accessories /
Communications / Hyper Terminal menu.
4. For a new connection, run Hypertrm.exe file.
5. Give a name and choose an icon for the connection. (You do not need to make
a new connection every time. You can use this name for the future connections.)
6. Choose communication port in the new coming window (COM1 or COM2) whichever
you have used in Step 1.
7. Port settings should be as follows:
Bits per second : 115200
Data Bits : 8
Parity : None
Stop bits : 1
Flow control : None
8. Now Hyper Terminal connection is established. From “Transfer” menu, choose
“Send File”.
9. Enter file name to be sent.
10. Choose Xmodem1K as protocol type.
11. Plug in the mains cord of the set to the mains supply just after pressing
Send button at the hyper terminal window. You will see the progress on the PC
screen. Besides, front panel display of the receiver will count the downloaded
packets.
12. Wait for the transfer to be completed. Then, disconnect and exit from Hyper
Terminal window.
Receiver will automatically start on standby mode. After software initialization (it takes 5 second) finished you can turn on your digital set-top
box by pressing one of the standby button, up/down or numeric buttons on remote
control or up/down/standby button on the front panel.